Recent News
Grinding Discs Explained: Cut Faster, Finish Smoother
2025-04-23
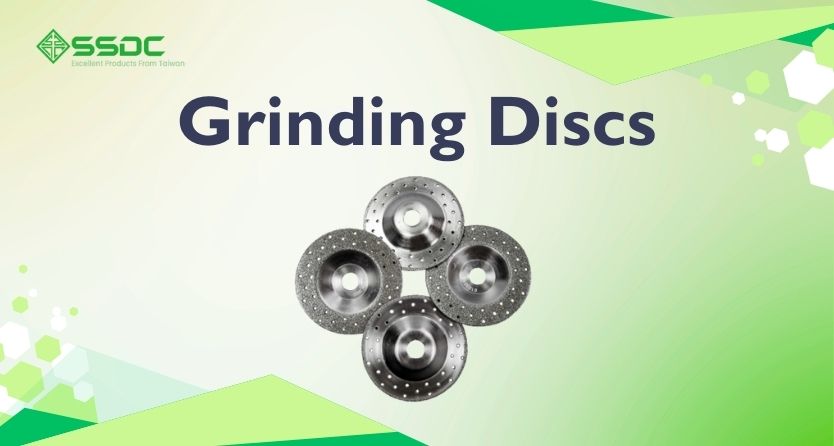
Introduction
In modern metalworking, construction, and precision fabrication, grinding discs are indispensable. Whether you're cutting, deburring, shaping, or finishing hard materials, these tools provide the durability and precision required for high-performance applications.
At Sea Shore Diamond Industrial Co., Ltd. (SSDC), we specialize in high-precision grinding solutions, including electroplated diamond grinding discs engineered for long service life and excellent cutting performance. In this article, we'll explore the benefits, types, and applications of grinding discs, and how to choose the right one for your needs.
What Are Grinding Discs?
Grinding discs are flat, circular abrasive tools designed to remove material by friction. Mounted on angle grinders, air tools, or bench grinders, they are essential for surface treatment, shaping, edge beveling, and precision grinding of various materials.
Depending on their bond type, grit size, and abrasive material, grinding discs can be used for tasks ranging from rough stock removal to fine surface finishing. They are available in a wide variety of sizes and configurations, making them highly adaptable for both industrial and workshop use.
Common Types of Grinding Discs
1. Metal Grinding Discs
These are commonly made from aluminum oxide or zirconia alumina and are ideal for steel, stainless steel, and aluminum. They provide aggressive cutting power and are widely used in fabrication shops for beveling, cleaning welds, and surface prep.
2. Diamond Grinding Discs
Bonded with industrial diamonds, these are designed for high-precision work on hard and brittle materials such as ceramics, glass, tungsten carbide, and stone. SSDC’s electroplated diamond discs are known for their sharp edges, fast material removal, and extended life.
3. Flap Discs
Composed of overlapping abrasive flaps, they are ideal for blending, deburring, and finishing after heavier grinding. They offer a balance between material removal and smooth surface finishes.
4. Cutting-Grinding Combo Discs
A versatile 2-in-1 tool, these discs combine the cutting capability of a thin cutting wheel with the grinding strength of a thicker disc—ideal for multitasking on the job site.
5. CBN Grinding Discs
Featuring cubic boron nitride abrasives, these discs are suited for high-speed steel and ferrous materials. They provide outstanding thermal stability, making them ideal for precision applications in tool and die grinding.
Industrial Applications of Grinding Discs
Grinding discs are crucial in a variety of sectors. Below are some of the most common applications:
- Metal Fabrication: Used for removing weld slag, chamfering edges, and smoothing surfaces before painting or assembly.
- Tool and Die Manufacturing: Ensures precision shaping of molds, punches, and cutting tools.
- Automotive: For grinding brake components, cutting suspension parts, and smoothing welded joints during repairs or fabrication.
- Construction: Applied in concrete grinding, tile cutting, and masonry shaping.
- Aerospace and Electronics: Used in surface grinding of high-hardness materials like ceramics and composites.
- Magnetic and Semiconductor Materials: Especially with electroplated diamond grinding discs, SSDC supports delicate substrate processing where surface flatness and minimal chipping are critical.
Why Choose High-Quality Grinding Discs?
Investing in premium grinding discs results in long-term savings and better product outcomes:
- Faster Throughput: Efficient material removal speeds up processing time.
- Lower Tool Wear: High-quality abrasives last longer and reduce tool change frequency.
- Improved Finish: Results in consistent, clean surfaces with less secondary polishing required.
- Increased Safety: Discs with balanced construction reduce vibration and are less likely to fracture under load.
- Versatility: A wide range of shapes, grits, and bonds allow you to tailor the tool to your specific material and process.
Tips for Selecting the Right Grinding Disc
To optimize performance and minimize downtime, consider the following when choosing a grinding disc:
- Material Type: Match the abrasive to the hardness and composition of the workpiece.
- Bonding System: Choose electroplated for precision and speed, or resin bond for smoother finishes.
- Grit Size: Coarse grits (60–120) for heavy removal; finer grits (180–400+) for polishing and finishing.
- Tool Compatibility: Check RPM limits, arbor hole size, and tool type (e.g., pneumatic, angle grinder, CNC).
SSDC's Grinding Disc for Pneumatic Use: Precision and Durability Combined
Among SSDC's grinding solutions, the Grinding Disc for Pneumatic Use is a high-performance solution engineered for use with air-powered tools. This compact electroplated diamond disc offers exceptional performance for:
- Surface flattening, edge trimming, and profile shaping on hard materials.
- Applications involving ceramics, magnetic substrates, tungsten carbide, and quartz.
- Lightweight design ideal for high-RPM pneumatic grinders.
- Available in various sizes and specifications to fit different machine setups.
Its electroplated construction ensures sharp cutting edges and consistent performance across its lifespan, making it a reliable choice for high-precision industries where tool control and dimensional accuracy are paramount.
Conclusion
Grinding discs are essential tools across industrial and technical fields, supporting efficient cutting, shaping, deburring, and surface finishing. Whether you're removing rust from metal, grinding ceramics to tight tolerances, or smoothing concrete joints, the right grinding disc makes all the difference.
At Sea Shore Diamond Industrial Co., Ltd. (SSDC), we are committed to helping professionals and manufacturers achieve their best work with our electroplated diamond grinding discs. Our Grinding Disc for Pneumatic Use represents the fusion of compact design, sharp cutting power, and long-lasting durability—backed by years of abrasive tool development experience.
Contact us today to learn more about SSDC's full range of grinding disc solutions or request a custom configuration tailored to your specific needs.